Power transformers are the vital components that ensure electricity flows smoothly through the grid, and their reliability is crucial. Power transformer monitoring solutions provide the eyes and ears necessary to keep these essential assets in optimal condition. By employing real-time data collection, expert analysis, and proactive measures, power transformer monitoring systems help you avoid costly downtime and extend the life of your transformers. Discover how these technologies are safeguarding the heart of electrical networks across the globe.
Monitoring Transformer Bushings
Monitoring transformer bushings is critical, because bushings are constantly under high stress due to the line voltage and heat effect of current flow. These stresses can be further aggravated by the presence of micro cracks from manufacturing, loss of mechanical strength due to ageing, repeated thermal cycling (load + sun), pollution and external flash over melting the porcelain, sludge and moisture in the insulating oil, and by the fact that new bushings have been made closer to design limits in order to reduce cost, size and weight.
These stresses can cause the insulation of the bushing to deteriorate. If left undetected, this can lead to catastrophic failure in more than half the cases,with violent explosions, large oil fires and broken shards of porcelain flying about. This can result in the total loss of the transformer, collateral damage to nearby equipment, human injuries, environmental claims and fines or contractual penalties.
For years, testing bushings meant taking a transformer off-line on a regular basis and closely inspecting the bushings for cracks or imperfections, monitoring the internal oil levels, measuring capacitance within the bushing itself (C1) or measuring the power factor (or tan-delta).
Taking a transformer off-line makes this approach impractical, thus minimizing the frequency of testing to once every few years. A critical problem can easily develop in between checks. With modern fast electronics, continuous monitoring of transformer bushings can now be technically achieved. Remote access to the data allows for continuous on-line monitoring of bushings and is now regarded as “best practice” to better guard against catastrophic bushing failure.
Intellix BMT 330 Bushing Solution
The Intellix BMT 330 continuously monitors the condition of bushings in real time and provides end users with the information they are used to receiving from off-line tests, namely changes in capacitance and power factor (tan delta), to assess the bushing dielectric efficiency and insulation integrity. Using state of the art custom made adaptors connected at the bushing tapping points, the Intellix BMT 330 measures:
- The change in bushing leakage current compared with the original values calculated from the bushing nameplate information and transformer operational voltage. As the change in current is proportional to the change in capacitance, the Intellix BMT 330 calculates the change in capacitance C1 of the bushing compared with when the bushing was installed, to gauge its dielectric capability and layer integrity.
- The timing differences between the 3 bushing current phases, which translate to phase angle differences relative to each other. Since a change of phase delay equates to a change in power factor, we can determine for each bushing the relative (compared to the others) change of power factor as a percentage of the nameplate value. This is used to gauge small deterioration of the bushing insulation.
- The Intellix BMT 330 measures ambient temperature, humidity and the temperature of the main tank. It correlates capacitance changes linked to thermal expansion of the bushing and compensates for the measurements being made at actual bushing operating temperature compared with nameplate values obtained off-line at 20°C.
Partial Discharge Detection
PD is a localized breakdown of a small portion of a solid or fluid electrical insulation system that is under high voltage stress, which does not completely bridge the space between two conductors. PD on solid dielectrics results in localized gradual erosion of the insulation system that eventually leads to failure of critical insulation.
Using the same bushing adaptors, the Intellix BMT 330 offers the added advantage of measuring high frequency signals in order to monitor PD activity, giving an added level of protection for the main tank of the transformer.
The amplitude of the PD pulses are recorded and used to calculate an overall measure of PD activity. Several methods are used to discriminate between internal PD and external noise (corona discharge). The BMT 330 also provides Partial Discharge Phase Resolve (PDPR) diagnostics.
Example of GE’s Intellix BMT 330 Solution Installed On a Three-Phase Transformer
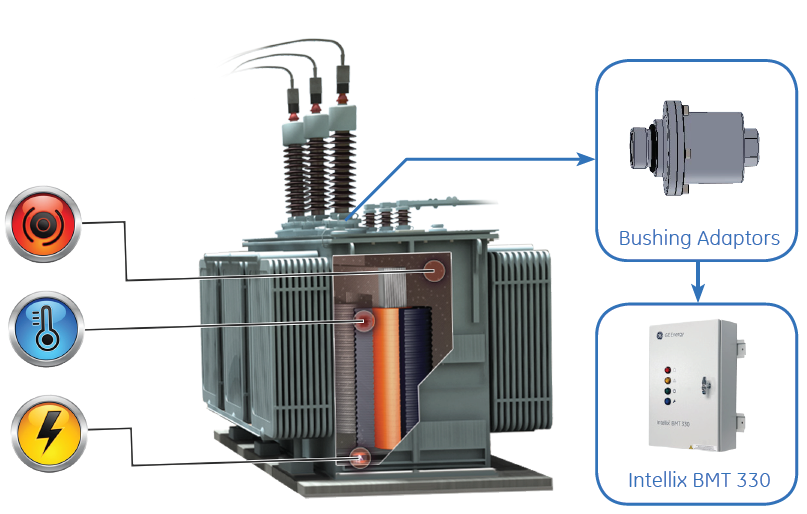
- Gas analyzer classifies the fault types, providing valuable insights into the transformers condition.
- Transformer aging can be calculated so that expensive failures can be avoided.
- Transformer faults are detected in their infancy, enabling fast remedial response.
- Through the same bushing tapping points, the Intellix BMT 330 monitors bushing insulation health and checks for presence of PD activity.
- Monitors up to 2 sets of 3 bushings per Intellix BMT 330.
- Advanced discrimination using additional sensors
GE’s Integrated Solution
- Intellix BMT 330 with Kelman TRANSFIX DGA
The Intellix BMT 330 can easily be integrated with GE’s Kelman TRANSFIX DGA analyzer, giving the end user a unique all-in-one solution that provides a more comprehensive view of the transformer’s overall condition, from bushing diagnostics and PD, to complete main tank monitoring.The Kelman TRANSFIX is an 9-gas on-line transformer monitoring unit. Using specially developed advanced photo-acoustic detection technology, the TRANSFIX measures all significant fault gases.
- Increased Asset Reliability
Having an all-in-one integrated solution from GE will significantly increase the ability to detect potential transformer problems at an early stage. The system will provide status on:
• Deterioration of the bushing insulation
• Partial discharge activity
• Moisture content in oil
• Developing key fault gases H₂, CO, C₂H₂, C₂H₄, C₂H₆, CO₂ and CH₄
This helps to decrease the risk of unplanned downtime and improve network reliability.
- Perception Fleet Software
GE’s Perception Fleet software allows an operator to easily download and visualize the data available from a critical transformer and use it to make better, more informed decisions. It offers ease of use, an intuitive interface, and familiar options that are common across all of GE’s Monitoring and Diagnostic products. The software is an upgradeable tool, allowing users to view all relevant transformer data from one centralized point.
With the Intellix BMT 330, Perception often uses a vector sum on a polar plot to easily highlight what is happening and eliminate common changesaffecting all bushings (load, temperature) that are not a source of concern.
- One-Vendor Solution Provider
Having a one-vendor providing the complete transformer monitoring solution can effectively lower installation costs, as well as reduce the administrative burden of coordinating various maintenance crews. All products work together and communicate seamlessly with no interface or responsibility issues.
GE has extensive experience and worldwide resources available to deliver integrated monitoring solutions and assist customers with transformer challenges, including installations, commissioning, training and on-going technical support.
Application Examples
On the left hand side the Intellix BMT 330 is connected to a 3 phase transformer. On the right hand side, the Intellix BMT 330 is being used on a bank of single phase transformers along with a spare transformer. Using external switches a spare transformer can be brought into service replacing one of the bank transformers without interrupting the grid.
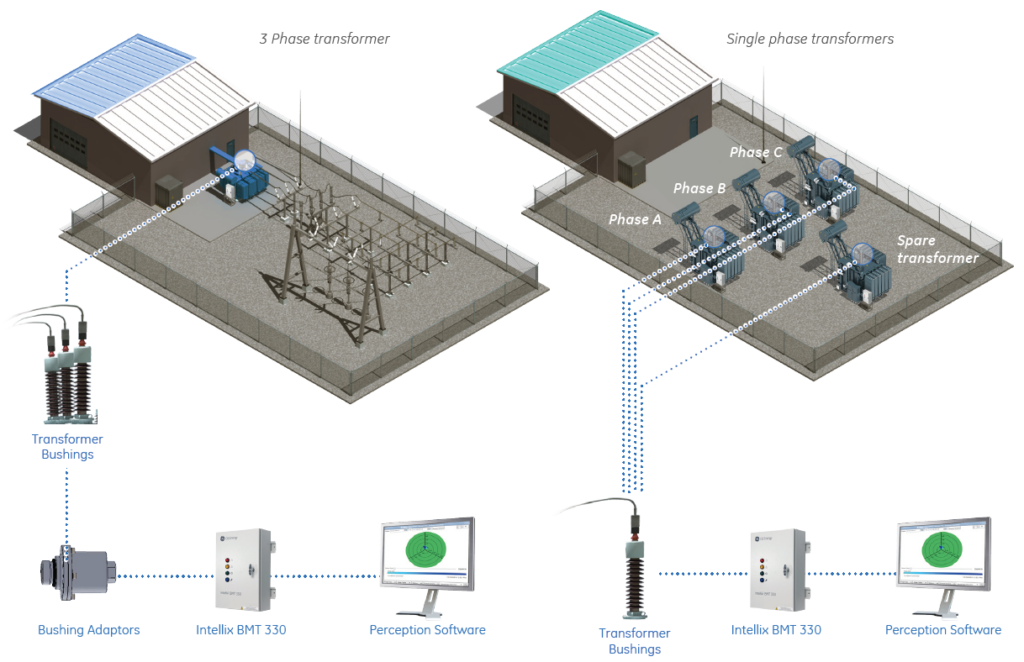
Power transformers are the workhorses of the electrical grid, playing a crucial role in ensuring a continuous and reliable supply of electricity. Any failure in these transformers can have significant consequences, leading to costly downtime and potential safety hazards. Power transformer monitoring has emerged as a powerful solution to address these challenges, providing real-time insights into the condition of transformers and enabling preventive measures. In this article, we will delve into the world of power transformer monitoring, exploring its significance, technologies, and the role it plays in ensuring the robustness of our electrical networks.
Importance of Power Transformer Monitoring
Power transformers are essential components in the electricity distribution network, responsible for stepping up or stepping down voltage to facilitate efficient power transmission. These transformers operate under varying loads and environmental conditions, which can lead to wear and tear over time. Monitoring their health and performance is critical for several reasons:
- Minimizing Downtime: Unplanned outages due to transformer failures can disrupt the electricity supply, affecting homes, industries, and critical infrastructure. Power transformer monitoring helps in identifying issues before they lead to catastrophic failures, allowing for planned maintenance and minimizing downtime.
- Ensuring Safety: Transformer failures can sometimes result in hazardous situations, such as oil leaks or explosions. Regular monitoring can detect potential issues and prevent safety hazards.
- Optimizing Performance: Monitoring systems provide valuable data that can be used to optimize the operation and maintenance of transformers, extending their lifespan and efficiency.
Role of Bushing Monitoring and Partial Discharge Detection
Bushing monitoring is a crucial aspect of power transformer health assessment. Bushings are the insulating devices that allow electrical conductors to pass through the transformer tank without any leakage. A failure in these bushings can lead to catastrophic consequences, making their continuous monitoring essential.
GE’s IntellixTM BMT 330 is an advanced online system designed to monitor the condition of bushings continuously. It not only monitors bushings but also detects developing partial discharge (PD) activity within the transformer main tank. Here’s how these technologies play a significant role:
- Early Fault Detection: The Intellix BMT 330 can detect impending failures at an early stage. By continuously monitoring the condition of the bushings, it can provide timely alerts to personnel, allowing for prompt action.
- Health Information: The system offers vital health information about both the bushings and the transformer. This data is invaluable in making informed decisions regarding maintenance and potential replacements.
- Integrated Solution: The Intellix BMT 330 can be used as a standalone system for bushing and PD monitoring, or it can be integrated with GE’s KelmanTM TRANSFIX Dissolved Gas Analyzer (DGA) multigas analyzer and PerceptionTM Fleet software. This integration provides a comprehensive view of the transformer’s condition and helps identify the root causes of major failures.
Key Benefits of Power Transformer Monitoring
The benefits of implementing a robust power transformer monitoring system, such as GE’s IntellixTM BMT 330, are far-reaching:
- Comprehensive Monitoring: The system offers comprehensive monitoring of transformer bushings and PD activity. It is capable of monitoring a 3-phase transformer or a bank of three single-phase transformers.
- Integration: The ability to monitor both bushings and PD activity using the same system streamlines the monitoring process and provides a holistic view of the transformer’s health.
- Diagnostic Software: GE’s Perception software is used for analyzing bushing information, PD activity, and DGA data. It simplifies data analysis and provides user-friendly insights.
- Single Supplier: Choosing a single supplier for the installation, servicing, and communication of these monitoring systems reduces administrative burdens and lowers the total cost of ownership.
Who are We?
Manufacturer |
Supplier |
Trader |
Importer |
Exporter |
Company |
Solution |
Where do we have clients and supply our Power Transformer Monitoring ?
India | United Arab Emirates | Uganda |
Nepal | Israel | Tanzania |
Vietnam | Egypt | Angola |
Philippines | Yemen | Kambia |
Indonesia | Turkey | Malawi |
Malaysia | Sudan | Botswana |
South Korea | Algeria | South Africa |
Oman | Monaco | Zimbabwe |
Iran | Nigeria | Cambodia |
Saudi Arabia | Ethiopia | Australia |
Namibia | Greece | USA |
Advantage of Power Transformer Monitoring
Power transformer monitoring is a proactive approach to ensuring the reliability and performance of transformers in electrical networks. It offers numerous advantages that contribute to the efficiency and safety of power distribution systems. Let’s explore the key benefits and advantages of power transformer monitoring:
- Early Fault Detection: One of the most significant advantages of power transformer monitoring is the early detection of faults and potential issues. By continuously analyzing data from various sensors and diagnostic tools, operators can identify problems in their infancy. This early warning allows for timely intervention and maintenance, reducing the risk of catastrophic failures and unplanned outages.
- Minimized Downtime: Power outages can have severe consequences for both consumers and industries. Monitoring systems help minimize downtime by detecting faults before they lead to transformer failures. This allows operators to schedule maintenance during off-peak hours, reducing disruptions to electricity supply.
- Safety Enhancement: Transformer failures can pose safety hazards due to factors like oil leaks and explosions. Power transformer monitoring enhances safety by identifying conditions that could lead to these hazards. Preventive maintenance can be conducted to address these issues, reducing the risk of accidents.
- Extended Transformer Lifespan: Monitoring provides valuable data about the transformer’s health and performance. This data helps in optimizing operation and maintenance practices, which can extend the transformer’s lifespan. By addressing issues early and reducing stress on the transformer, asset owners can get more value from their investments.
- Cost Reduction: The early detection of issues, predictive maintenance, and optimized operation lead to cost reductions. Power transformer monitoring helps reduce maintenance costs by avoiding costly emergency repairs. Additionally, it optimizes the use of resources, ensuring that maintenance activities are carried out when they are most cost-effective.
- Data-Driven Decision Making: Monitoring systems generate a wealth of data about the transformer’s condition. This data can be analyzed to make informed decisions about the operation, maintenance, and potential replacements of transformers. Data-driven decision-making ensures that resources are allocated efficiently.
- Integration with Diagnostic Tools: Some power transformer monitoring systems, like GE’s IntellixTM BMT 330, integrate seamlessly with other diagnostic tools, such as dissolved gas analyzers and partial discharge detectors. This integration provides a holistic view of the transformer’s condition, allowing operators to pinpoint the root causes of major failures.
- Efficient Maintenance: Power transformer monitoring systems help optimize maintenance schedules. Maintenance can be performed when it is needed rather than on a fixed time-based schedule. This ensures that resources are used efficiently and that transformers are maintained at their peak performance.
- Streamlined Communication: Choosing a single supplier for the installation, servicing, and communication of monitoring systems simplifies the process. It minimizes administrative burdens and ensures that all components work seamlessly together, reducing the total cost of ownership.
- Enhanced Reliability: Ultimately, the advantage of power transformer monitoring is enhanced reliability. By identifying and addressing issues before they lead to failures, power distribution systems become more reliable and can meet the ever-increasing demands for electricity with confidence.